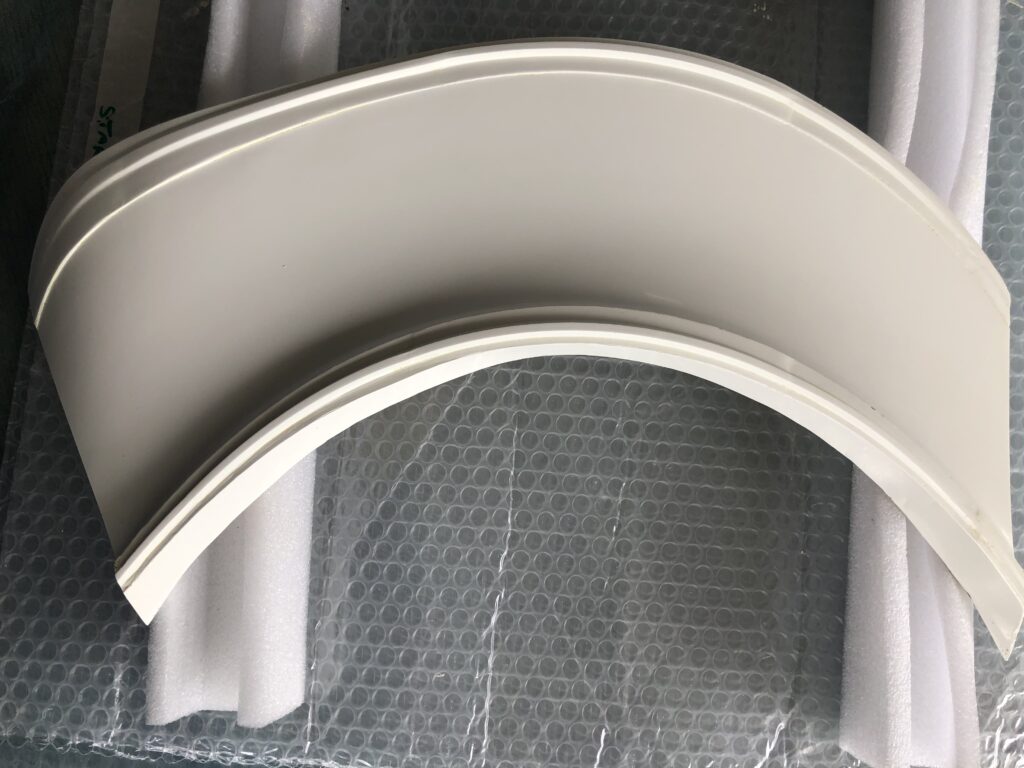
Complete section 4 of 8 for moulding starboard wings.
A drone without wings, to exploit quick-response rotors sooner, is the current priority, so progress on the winged model and it’s starboard wing will be slow for now.
Complete section 4 of 8 for moulding starboard wings.
A drone without wings, to exploit quick-response rotors sooner, is the current priority, so progress on the winged model and it’s starboard wing will be slow for now.
Weight of wing #2 is 335 g. Hack-sawed in half to inspect internal hollow structure.
Hollow channels form structural shear-webs, and are also suitable for threading cables.
I am still experimenting with alternative layups and infusion procedures. Wing #3 was a failure.
Hot from the mould: a port wing!
#1 a surprise success after infusion mishaps! It has many flaws but is actually usable! Weight is 561 grams. Potentially only 250 grams with these materials and methods. So there’s scope for improvement by using far less resin: The skin is already extremely thin, enough to meet the 250 gram target.
The bad news: There is no mould yet for a starboard wing. And the port mould took a year to make! Who can afford CNC machining?
The test-wings are too expensive, and unnecessarily heavy, to be suitable for production. We expect to crash a few prototypes! So our plan is to make carbon-fibre moulded copies of the test-wings. I have made a mould for the port wing (unsealed below), and it has held a vacuum gauge steady for 54 hours now: I think the seal is excellent. So far so good, but an awful lot of work remains to test convenience of a moulding cycle. And first, I need to reinforce to mould to withstand the pressure when empty. I ran this test with the wing plug inside to support it against the air-pressure load.
See the vacuum test at https://www.instagram.com/p/Crh2p7VMjc0/
Results of a second test of the 5-blade variable-pitch rotor
Rotor diameter is 410 mm.
Elastic tailoring is 20% more compliant than in the first test, to give 3 degrees more blade pitch-up at maximum torque.
Elastic elements of different spec. are easily swapped.
This test shows rotor speed levelling out at around 3500 RPM as lift continues to increase with power due to increasing blade pitch.
The batteries hold up better than in the previous test. I don’t know why. Perhaps they needed a rest!
See a video of this test at https://www.instagram.com/agileaircraft/
The advantages of this design are
1) Extremely quick response. A conventional drone must spin each rotor faster to get more lift, for example to counter a random wind gust.
A drone or aircraft with far quicker response could be used in new ways, such as very close to structures in windy conditions.
2) Low vibration in forward flight. Each lift-rotor blade generates more lift when advancing than when retreating, but in a 5-bladed design, the forces cancel.
3) Low noise. For the same lift and diameter, 5-blades run slower and consequently quieter than 2-blades.
4) Auto-rotation by default. For safety and simplicity, the default blade pitch is negative when not powered. The blade pitch range is readily adjustable to suit application requirements.
Some test results are shown here. The current plan is to build and test a 5-bladed version. Although this will be more expensive than the 2-bladed version, the advantages for achieving our goals are decisive.
A revised lift-rotor is being made. The original test rotor works well, but was difficult to make. The Mk 2 is intended to be more suitable for production, but is functionally the same.
A new hub body was 3-d printed, and is also intended to be suitable for injection moulding.
But I do not know any supplier who can print suitable plastic to 0.05 mm repeatable accuracy. Any suggestions? So re-finishing of bearing seats has been necessary.
JTC Model Technologies have supplied excellent prototype aluminium components and steel broaching tools for the new rotor. Their parts fit beautifully, they are very helpful, and Alice has first-rate command of technical English. So it doesn’t matter that I have zero command of Chinese!
Earlier, JTC Model Technologies also machined wing mounts from blocks of ABS. Although there was some post-machining distortion, these proved to be an excellent way to quickly mount the wings for testing. Strong enough to hold 20 kg of lift plus road shocks and wind-gusts!
The picture shows a half-mould plug expertly printed in ASA plastic by Steve at Reality Printing, Toowoomba, QLD, Australia. The print is nearly 1m long, printed in 3 sections with an alignment grove on the back. ASA plastic was chosen to withstand the curing temperature of a glass-reinforced mould.
This plug is an exact scale model of the fuselage shown in the home page image. We need to polish the plug and use it to make a mould for fuselages of model drones. Tail length and access hatches may be customized later.