Rigid lift-rotor blades each generate more lift when advancing than when retreating. But remarkably I think, it is possible for the net oscillatory loads at the rotor hub in an idealised aerodynamic model to cancel if there are enough blades.
APPROXIMATIONS of an idealised rotor model
- The blades have a high aspect ratio, are of linearly-tapered section along their length, are perfectly rigid, identical, and evenly spaced around the rotor hub.
- The Reynolds number (chord) is large, angle of attack small, and the lift of blade elements are independent and proportional to angle of attack.
- In the case of blades of uniform section, both the effective angle-of-attack and lift coefficient of blade n each change with rotational phase by a factor cos(βn) due to a local blade-sweep angle βn, because the length of chord-sections parallel to the local relative velocity change by a factor 1/cos(βn) , and the component of length of the blade normal to the local relative velocity changes by the factor cos(βn). The case of linearly-tapered sections is complicated by an additional tapering angle, but the net cancellation of oscillatory loads is the same.
- All other effects are ignored.
Figure 1 shows an example , for a 5-bladed version of this idealised rotor model, a single cycle of thrust load, roll torque, and pitch torque for individual blades and their net sums at the hub. The net loads are steady, with zero net oscillatory forces. In this example, the vehicle is advancing parallel to the plane of the rotor, such as horizontal flight with a level lift-rotor.
Oscillatory forces do not all cancel in the case of 1,2,3, or 4-bladed rotors.
The general rule appears to be that oscillatory blade-forces will cancel at the hub if there are more than N blades and the rotor forces can be expressed as a polynomial of degree N in sines and cosines of the rotational phase angle. Since any continuous periodic function can be approximated arbitrarily well in this way, this general rule implies that hub vibration of a rigid rotor can be reduced below any specified level simply by having enough blades.
Our conclusion is that at least 5 blades are needed to avoid severe vibration of a rigid rotor, but more than 5 blades is increasingly difficult to manufacture, with probably much less benefit.
Figure 1: A single cycle of oscillatory blade-forces. Vehicle advancing at 10 m/s. Rotor speed 500 RPM.
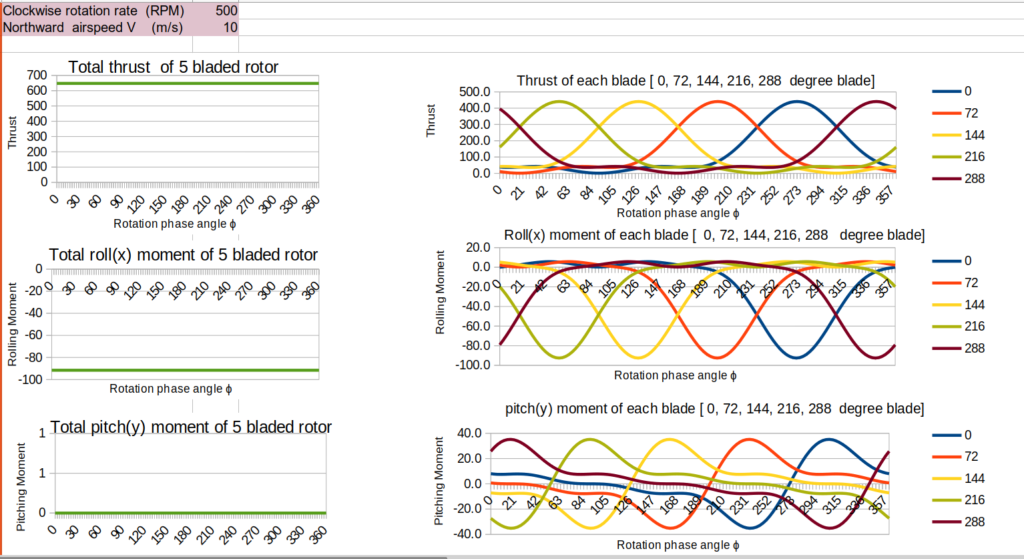